اولین مرحله ساخت خودرو: بدنهسازی و تولید خودرو
آشنایی با مراحل تولید یک خودرو به قلم فربد زاوه
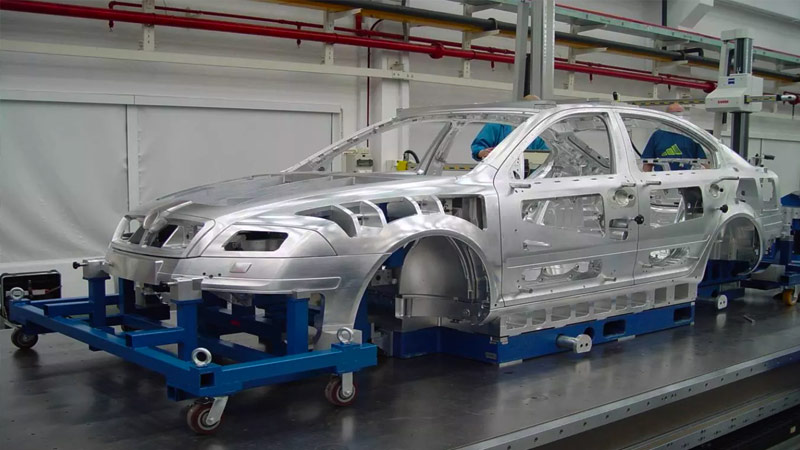
اولین مرحله ساخت خودرو، بدنهسازی است. هرچند بسیاری از کارخانههای بزرگ واحد پرس دارند، اما تولید قطعات بدنه در پرس شاپ و موتور در موتورسازی، قطعهسازیهای داخل خودروساز محسوب میشود، اما بدنهسازی، اولین مکانی است که خودرو در آن شکل میگیرد و نخستین گام در فرآیند خودروسازی است. خطوط بدنهسازی معمولا از سه بخش اصلی تولیدی و یک بخش کنترل کیفی تشکیل میشوند.
در بخش اول، قطعات پرسی به یکدیگر متصل میشوند و مجموعههای اصلی بدنه را شکل میدهند. برای اطمینان از صحت اتصال و یکسان بودن مجموعه های تولیدی، عملیات تولید مجموعه ها در جیگهای فرعی انجام میشود که اصطلاحا Sub-Jig نامیده میشوند. یک خودرو ممکن است دهها جیگ فرعی داشته باشد که مجموعههایی مانند درهای جانبی، کف خودرو Underbody، پنلهای جانبی Side Panels، درب موتور و صندوق و سایر مجموعههای اصلی توسط آنها تولید شود.
بیشتر بخوانید: آشنایی با مراحل ساخت و تولید خودرو
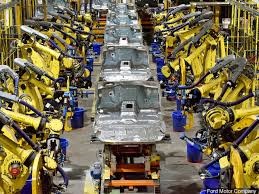
فرایند اتصال قطعات پرسی در خودروهای با بدنه فولادی جوشکاری حرارتی، قوس الکتریکی و یا لیزر است و برای قطعات آلومینیومی باید از فرایند پرچ و یا جوش لیزر (به واسطه ساختار متالورژیکی آلومنیوم) استفاده شود. نهایتا در قطعات کامپوزیتی، استفاده از چسب الزامی است. هرچند در برخی از خودروهای جدید با بدنه های آلومنیومی و فولادی هم برای اتصال قطعات پرسی از چسب استفاده میشود.
در برخی از قطعات مانند درها یا درب موتور، امکان جوشکاری به دلیل زیبایی بصری وجود ندارد. اثر جوشکاری بر روی سطوح فلزی میماند و برای از بین بردن آن نیاز است عملیات اضافه بتونه کاری یا پوست آب زنی انجام شود که هم جریان تولید را پیچیده، گران و کند میکند و هم زیبایی بصری را به شدت کاهش میدهد. برای فرار از جوشکاری در این قطعات، لبه پنل بیرونی که در دید قرار دارد بر روی پنل داخلی قطعه خم میشود. این امر که آن را Hemming مینامند، معمولا با اضافه کردن سیلر و چسب خمیری به محل اتصال همراه است و هم مانع ورود آب و جسم خارجی در دوره مصرف میشود و هم قطعه را یکپارچهتر و مستحکمتر میکند. عملیات لب برگردانی نیازمند تحهیزات خاص و بسیار دقیقی است که قطعه نهایی کیفیت مطلوبی داشته باشد.
در بخش دوم، با استفاده از یک جیگ اصلی (که Main Jig یا جیگ مادر هم نامیده میشود) چهار مجموعه اصلی کف، پنلهای جانبی و سقف به یکدیگر متصل میشوند. خروجی جیگ اصلی یک اتاق کامل است. با توجه به اینکه بدنه خودرو از این مرحله تقریبا کامل شده است، برای نقل و انتقال بر روی گاریهای مخصوصی قرار میگیرد که اسکید Skid نامیده میشود. استفاده از خطوط انتقال خودکار یا کانوایرها از مرحله شروع میشود که میتواند بر روی زمین یا سقف نصب شده باشد. در سالنهای بدنه سازی، استفاده از کانوایرهای زمینی متداولتر است.
بیشتر بخوانید: آیا خودروسازان بزرگ دنیا به ایران برمیگردند؟
برای ادامه تولید بعد از جیگ اصلی، بدنه وارد مرحله اخر اتاق سازی میشود و قطعات باقیمانده مانند درها، درب صندوق و موتور با اتصال پیچ و مهره به بدنه متصل میشوند و نهایتا بدنه خودرو تکمیل میشود. معمولا خودروسازانی که قطعات را به صورت منفصله دریافت میکنند، از مرحله دوم بدنهسازی فعالیت تولیدی خود را آغاز میکنند و تولید مجموعهها در همان شرکت مادر انجام میشود. به همین دلیل، ظرفیت خطوط فرعی بالاتر از خطوط اصلی است. در خودروهای پرتیراژ، وجود دو یا چند جیگ اصلی گریزناپذیر میشود.
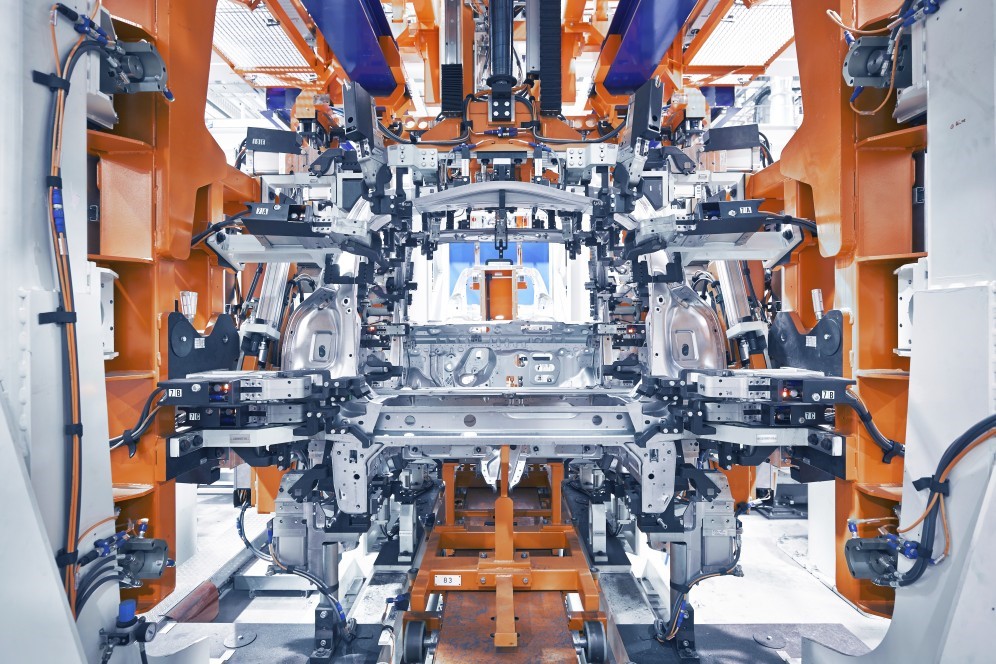
شرکتهای خودروسازی برای کنترل کیفیت بدنههای ساخته شده، سیاستهای گوناگونی دنبال میکنند اندازه گیری دقیق قطعات به صورت اتفاقی و انتخابی یک روش متداول و سنتی است. امروزه شرکتهای صاحب نام، با استفاده از فناوریهای هوش مصنوعی و عکس برداری دیجیتال، کنترل کیفی ابعادی را در مقیاس بالاتر و سرعت بیشتری انجام میدهند. تست مقاومت جوش هم تست مهم دیگری است که مکررا انجام میشود. متناسب شرایط خط تولید، اتاق و قطعات جوشکاری شده، در دستگاه کشش قرار میگیرند تا میزان مقاومت جوش اندازه گیری شود تا از ایمنی مناسب بدنههای تولیدی اطمینان حاصل شود.
در این نوع تست که تست مخرب محسوب میشود، قطعات از خط تولید به صورت رندم انتخاب میشوند و نهایتا با اعمال نیرو، آستانه تحمل نیروی کشش را تا انهدام قطعه و جوش اندازه گیری میکنند تا از قرار داشتن مقاومت قطعه و جوش در بازه استاندارد طراحی، اطمینان حاصل کنند. سپس، در صورت بروز اشکلات اساسی در مقاومت قطعات، ممکن است حجم زیادی از قطعات و بدنههای ساخته شده مهر قرمز بدنهسازی دریافت نمایند که شرکتهای صاحب نام، حتی اجازه مصرف آن را به عنوان قطعات یدکی نمیدهند و قطعات امحا شده و به صورت فلز قراضه فروخته میشوند. درصورتی که مشکل کیفی گزارش نشود، بدنه های تولیدی شماره سریالی دریافت میکنند که تا آخر عمر خودرو، مرجع شناسایی آن میشود. شماره شاسی یا اصطلاحا VIN در این مرحله در محلهای از پیش تعریف شده حک میشود.
بیشتر بخوانید: ما همه میرزاخانی هستیم!
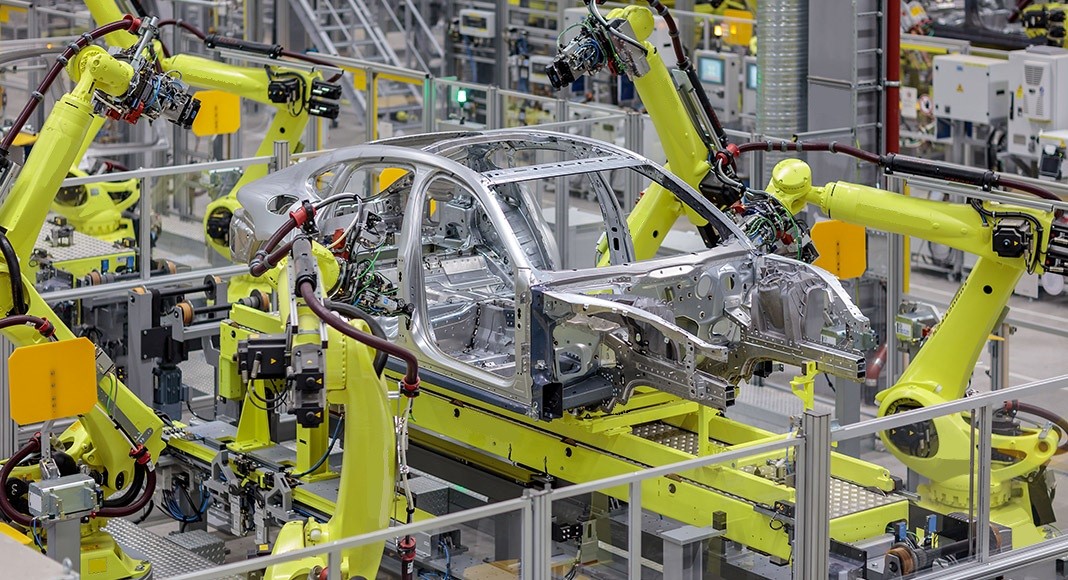
با توجه به آسیب پذیر بودن فولاد در برابر هوا و احتمال پوسیدگی قبل از رنگ آمیزی و همچنین، احتمال بالای آسیب بدنه های تولید شده، خروجی سالنهای بدنهسازی به صورت مستقیم وارد سالن رنگ میشود تا میزان آسیب به بدنه های تولید شده در اثر انبارش به حداقل برسد. البته برای اجتناب از توقف زنجیره تولید در اثر حوادث پیشبینی نشده و خرابی تجهیزات انبارهای میانی بین هر دو مرحله اصلی تولید خودرو پیش بینی میشود. خودرویی که از بدنه سازی خارج شده است چون فاقد رنگ است، اصطلاحا به آن بدنه سفید میگویند و لذا انبار انتهای سالن بدنهسازی و قبل از رنگ را White Body Storage یا WBS مینامند.